Component Services
Column Attach
Six Sigma Microelectronics has been performing Column Attach services since 1998 and has attached over 150 million solder columns for aerospace applications.
Solder columns are tiny pins (made primarily of solder) attached to integrated circuits (ICs); these ICs are then mounted to a printed circuit board (PCB). Solder columns are used in different devices, such as PowerPCs, FPGAs (Field Programmable Gate Arrays), and ASICs (Application Specific Integrated Circuits). These FPGAs and ASICs have connection-counts between 1,000 and 2,500 per device.
There are several types of solder columns. Copper-reinforced solder columns* are the industry favorite due to the significant thermal and mechanical improvement over other solder column designs (i.e., IBM-style straight-wire). These solder columns are very ductile, which helps them to absorb the solder joint stress. In a straight-wire column, a crack quickly propagates, causing an electrical open. However, with Six Sigma solder column’s unique construction, the electrical open is abated by the redundant connection created by the copper ribbon.
Six Sigma is the column attach supplier for the majority of domestic FPGA and ASIC manufacturers used in space applications. For over 25 years, Six Sigma has also been the near-sole supplier for solder columns on PowerPCs for numerous non-space applications such as M1A2 tanks, F-16’s, F-18’s, TOW missiles, UAVs, etc.
Six Sigma has achieved an enviable position of market dominance by decades of innovation, hard work, and continuous improvement. It has outperformed in the marketplace by keeping honesty and long-term reliability of the valuable devices it handles at the forefront of all of its decision-making. The experience and knowledge base that exists at Six Sigma cannot be found anywhere else in the US electronics manufacturing infrastructure.
Six Sigma has been manufacturing its own solder columns since 1996 and performing its column attach service since 1998. Six Sigma has spent decades and millions of dollars optimizing its solder column technology. It is critical that both the solder columns and column attach be manufactured and performed by a QML-certified entity, with a knowledgeable team that has a full understanding of the process-related risks.
Six Sigma’s solder column manufacturing and column attach lines are QML-Q, V, & Y certified by DoD’s Defense Logistics Agency (DLA).
*Originally designed by Raychem Corporation in 1984 and purchased by Six Sigma Microelectronics in 1996.
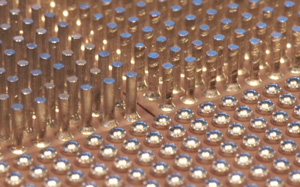
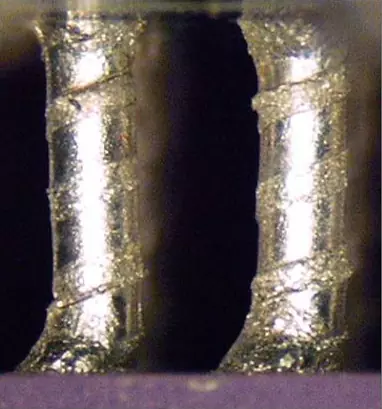

Ball Attach & Reballing
In 2006, the European Union implemented the RoHS initiative where hazardous substances, including lead (Pb), were banned from commercial electronics. With the commercial market’s move to Pb-free solders, this “Pb ban” resulted in a diminished supply of Tin-Lead (Sn-Pb) BGA devices in the military and aerospace industries. There were also reliability concerns associated with mixed assemblies, where Sn-Pb BGAs were used in lead-free boards, and vice versa. These concerns prompted the military and aerospace industries to reball these lead-free BGAs back to Sn-Pb.
Six Sigma has been performing Ball Attach and Reballing services since 1997 and has processed over 3 million BGA devices. Six Sigma offers three methods of BGA reballing based on volume:
- Preform Method: Low-volume
- Tooling Method: Mid-volume
- Automated Method: High-volume
Six Sigma can also reball different solder alloy compositions: Sn63-Pb37, Sn10-Pb90, Pb-free (SAC305, SAC105, SAC405), specialty alloys typically provided by the customer (SACX), etc.
Hot Solder Dip (Robotic)
Six Sigma Microelectronics is the industry leader in hot solder dipping of devices. This method is used to change the termination finish of devices from lead-containing to lead-free or vice versa. It is currently one of the strategies being used to mitigate tin whiskers, which can form when pure tin plating is used. Hot solder dipping of pure tin-finished terminations using tin-lead (Sn-Pb) solder reduces tin whisker formation by replacing tin with a tin-lead alloy. It is very important that no pure tin remains on the devices. Hot solder dipping of tin-finished leads with lead-free alloys such as tin-silver-copper (SAC) also reduces whisker formation. Although not as effective as lead, so far there is no evidence that these SAC alloys produce whiskers.
Hot solder dip applies to almost all types of devices. There are several reasons why devices are solder dipped. The method is used to change the lead finish (i.e., from lead-free to leaded, or from leaded to lead-free). It is also used to improve/restore the solderability of the parts, and can act as the primary finish for the terminations.
